Learn how plastic extrusion boosts production efficiency
Learn how plastic extrusion boosts production efficiency
Blog Article
Comprehending the Basics and Applications of Plastic Extrusion in Modern Production
In the world of modern production, the technique of plastic extrusion plays a critical duty - plastic extrusion. This intricate process, entailing the melting and shaping of plastic with specialized dies, is leveraged across numerous markets for the development of diverse items. From auto parts to durable goods product packaging, the applications are substantial, and the possibility for sustainability is similarly excellent. Unwinding the principles of this procedure exposes the true versatility and possibility of plastic extrusion.
The Principles of Plastic Extrusion Refine
While it may show up facility, the principles of the plastic extrusion process are based upon reasonably straightforward principles. It is a production procedure where plastic is thawed and after that formed right into a constant profile with a die. The raw plastic material, usually in the type of pellets, is fed right into an extruder. Inside the extruder, the plastic goes through warm and stress, creating it to melt. The liquified plastic is then forced through a designed opening, referred to as a die, to develop a long, constant item. The extruded product is cooled and afterwards reduced to the desired size. The plastic extrusion procedure is thoroughly used in various industries because of its flexibility, efficiency, and cost-effectiveness.
Different Sorts Of Plastic Extrusion Strategies
Structure upon the basic understanding of the plastic extrusion process, it is needed to check out the various methods associated with this manufacturing method. Both main methods are profile extrusion and sheet extrusion. In profile extrusion, plastic is melted and created right into a constant account, often used to develop pipelines, poles, rails, and home window frames. In contrast, sheet extrusion produces large, flat sheets of plastic, which are commonly further processed right into items such as food product packaging, shower drapes, and cars and truck components. Each technique requires specialized equipment and accurate control over temperature level and pressure to make certain the plastic keeps its form during air conditioning. Understanding these methods is key to utilizing plastic extrusion efficiently in modern-day manufacturing.

The Role of Plastic Extrusion in the Automotive Industry
An overwhelming majority of components in modern-day vehicles are items of the plastic extrusion process. This process has changed the automotive industry, changing it into a more effective, economical, and versatile manufacturing sector. Plastic extrusion is primarily used in the manufacturing of numerous automobile elements such as bumpers, grills, door panels, and dashboard trim. The process supplies an attire, constant result, allowing makers to generate high-volume parts with great accuracy and marginal waste. The lightness of the extruded plastic components my review here adds to the general reduction in automobile weight, improving fuel effectiveness. The durability and resistance of these components to heat, cool, and influence improve the durability of cars. Thus, plastic extrusion plays an essential function in automobile manufacturing.
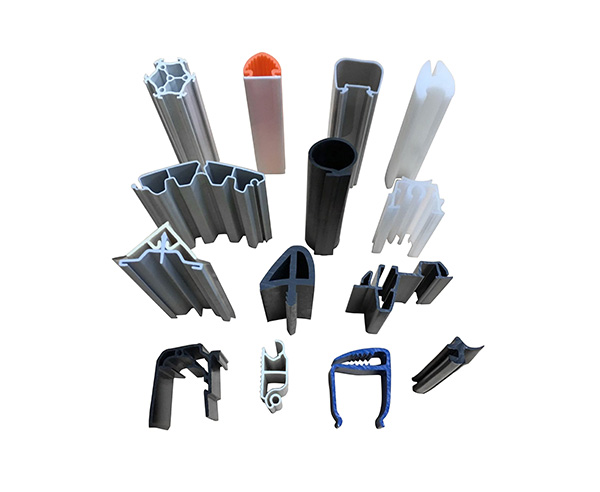
Applications of Plastic Extrusion in Customer Product Production
Past its substantial effect on the automobile sector, plastic extrusion proves equally reliable in the world of customer goods producing. This process is critical in creating a vast array of items, from food product packaging to family appliances, playthings, and even clinical devices. The flexibility of plastic extrusion permits suppliers to create and produce complicated forms and sizes with high precision and performance. Due to the recyclability of many plastics, extruded elements can be recycled, minimizing waste and expense (plastic extrusion). The adaptability, versatility, and cost-effectiveness of plastic extrusion make it a favored selection for many consumer products suppliers, adding dramatically to the sector's development and development. The environmental ramifications of this widespread usage call for cautious factor to consider, a topic to be reviewed better in the succeeding go to this site section.
Environmental Influence and Sustainability in Plastic Extrusion
The pervasive use plastic extrusion in producing welcomes analysis of its environmental implications. As a procedure that often utilizes non-biodegradable materials, the environmental influence can be substantial. Energy usage, waste production, and carbon exhausts are all issues. However, sector developments are enhancing sustainability. Reliable equipment reduces power usage, while waste monitoring systems recycle scrap plastic, lowering resources needs. In addition, the development of biodegradable plastics provides a more eco pleasant option. In spite of these improvements, better advancement is required to alleviate the ecological impact of plastic extrusion. As society leans towards sustainability, manufacturers need to adapt to remain feasible, stressing the importance of constant study and advancement in this field.
Verdict
In conclusion, plastic extrusion plays a crucial duty in modern manufacturing, specifically in the automotive and customer goods industries. Understanding the fundamentals of this procedure is essential to optimizing its benefits and applications.
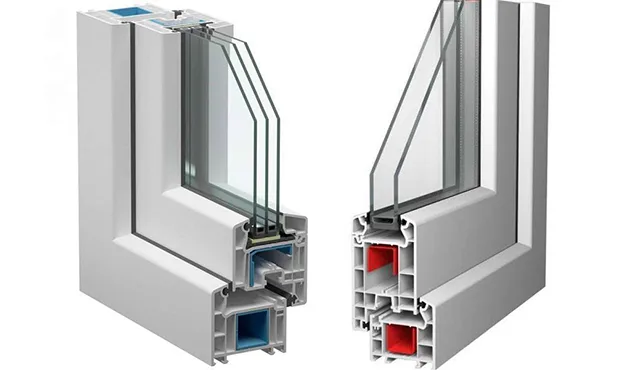
The plastic extrusion procedure is extensively utilized in different markets due to its efficiency, convenience, and cost-effectiveness.
Building upon the basic understanding of the plastic extrusion procedure, it is necessary to discover the different strategies entailed in this manufacturing technique. plastic extrusion. In comparison, sheet extrusion creates big, flat sheets of plastic, which are normally additional processed into products such as food packaging, shower curtains, and automobile click here for info components.A frustrating majority of components in modern lorries are products of the plastic extrusion procedure
Report this page